Understanding the residual capacities vs nominal capacities of a forklift is essential for safe and efficient operation. In this post, you will not only learn about residual and nominal capacities but you will also find out about key concepts that relate to forklift capacities such as how a forklift stays balanced, the role of the stability triangle, load centers, and how to read your forklift’s capacity plate. By the end, you’ll know how to calculate your forklift’s actual lifting capacity. Click on each section to learn more.
- How Does a Forklift Stay Balanced?
- What Is the Stability Triangle?
- What Is the Difference Between Residual Capacities and Nominal Capacities?
- What are Load Centers and Why Do They Matter?
- How to Read Your Forklift Capacity Plate
- What Is the Capacity of Your Forklift: Calculation
For more information on forklift capacities or help selecting the right forklift for your needs, contact Ri-Go Lift today. Our team is ready to assist with expert advice and tailored solutions!
Residual Capacities vs Nominal Capacities
1. How Does a Forklift Stay Balanced?
To understand forklift capacities, it’s essential to first grasp how a forklift maintains balance. A simple analogy is a teeter-totter (or seesaw), which balances two weights on either side of a central pivot point.
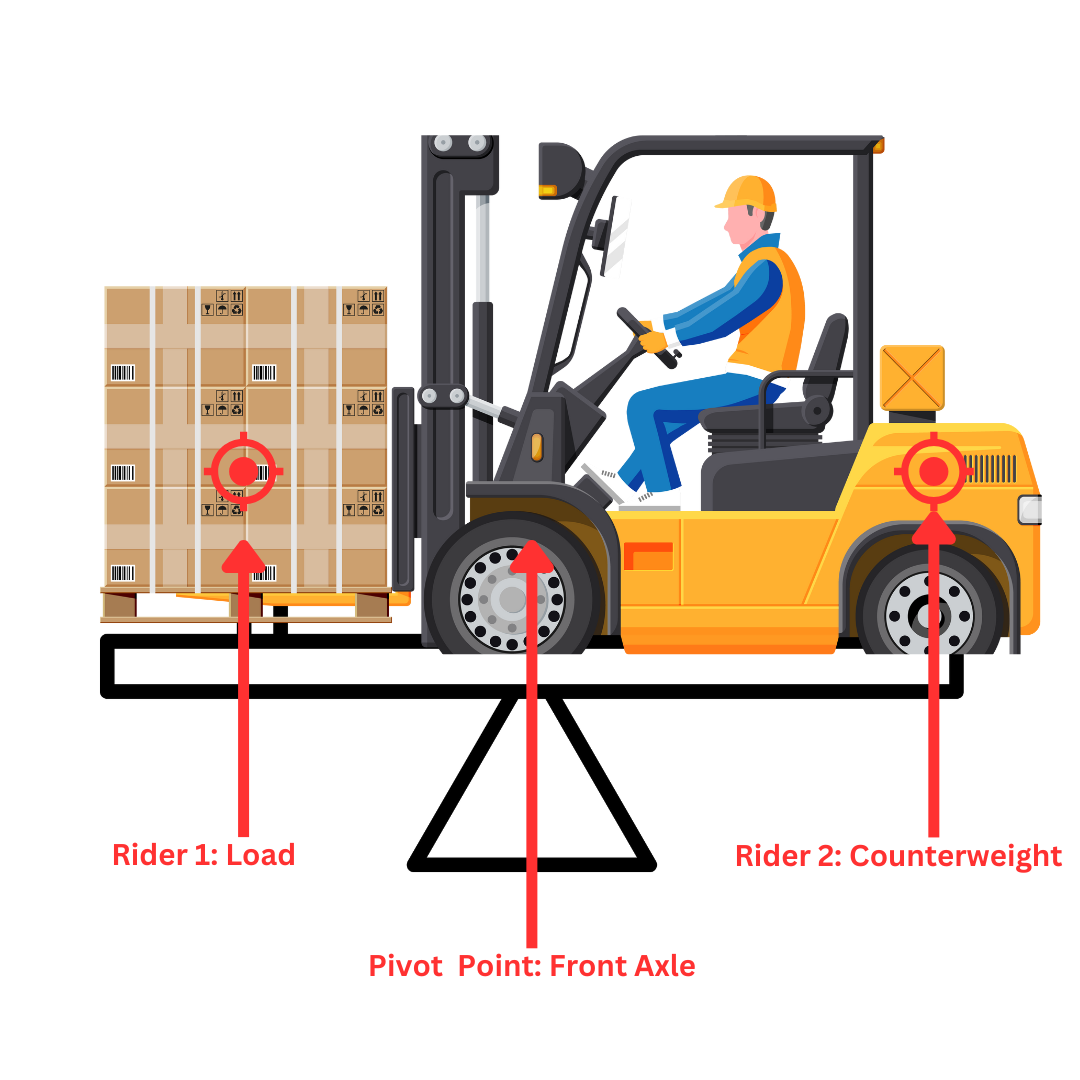
A forklift balances similar to a teeter-totter.
In a forklift, this same “teeter-totter” principle applies, with the front axle serving as the pivot point that balances the counterweight and the load being lifted.
The Pivot Point: The Forklift’s Front Axle
The front axle of a forklift acts as the central balance point, similar to the center of a teeter-totter. This is where the load at the front of the forklift and the counterweight at the rear strike a balance. When the load and counterweight are appropriately balanced, the forklift remains stable and won’t tip.
Rider 1: The Counterweight
The counterweight is a large metal block located at the rear of the forklift. Its primary function is to provide downward force to counterbalance the load being lifted at the front of the forklift. By offsetting the weight of the load, the counterweight helps prevent the forklift from tipping forward.
Rider 2: The Load-Bearing Mechanism and the Load
The load-bearing mechanism is the part of the forklift that handles and lifts the load. If the counterweight is one end of the “seesaw,” the load and its lifting mechanism are the other end. Properly balancing these two elements is crucial for safe forklift operation.
By maintaining balance across these three key points, a forklift can lift and transport loads safely without compromising stability.
2. What Is the Stability Triangle?
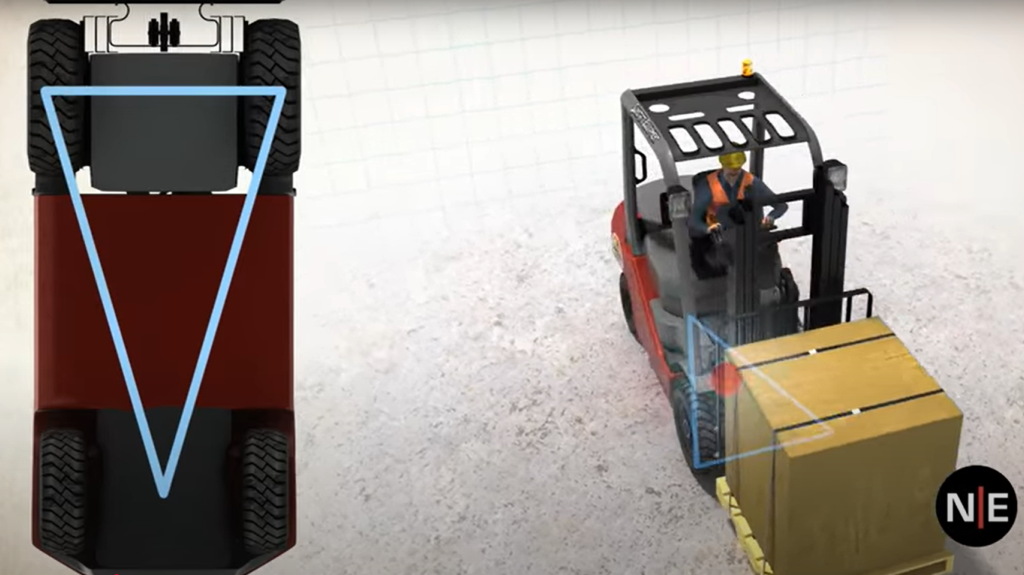
Residual Capacities vs Nominal Capacities: The stability triangle is formed between the center of the rear axle and both front wheels. Image Source: Nextedgevideo
The stability triangle is a key concept in forklift safety that illustrates how a forklift can operate without tipping over. This triangle is an imaginary shape formed between the center of the rear axle and both front wheels of the forklift. Understanding this triangle is essential for preventing tip-overs and ensuring proper load handling.
Why Is the Stability Triangle Important?
The stability triangle represents the three points where a forklift’s weight is supported: the rear axle’s center and the two front wheels. The position of the forklift’s combined weight within this triangle determines its stability. If the weight shifts outside the triangle’s boundaries, the forklift risks tipping over.
Key Concepts for Understanding the Stability Triangle
To fully grasp the stability triangle and how forklifts are designed to stay balanced, you need to understand five core concepts:
- Center of Gravity
- Combined Center of Gravity
- Load Center
- Load Moment
- Load Capacity
Let’s break down the first two.
What Is Center of Gravity?
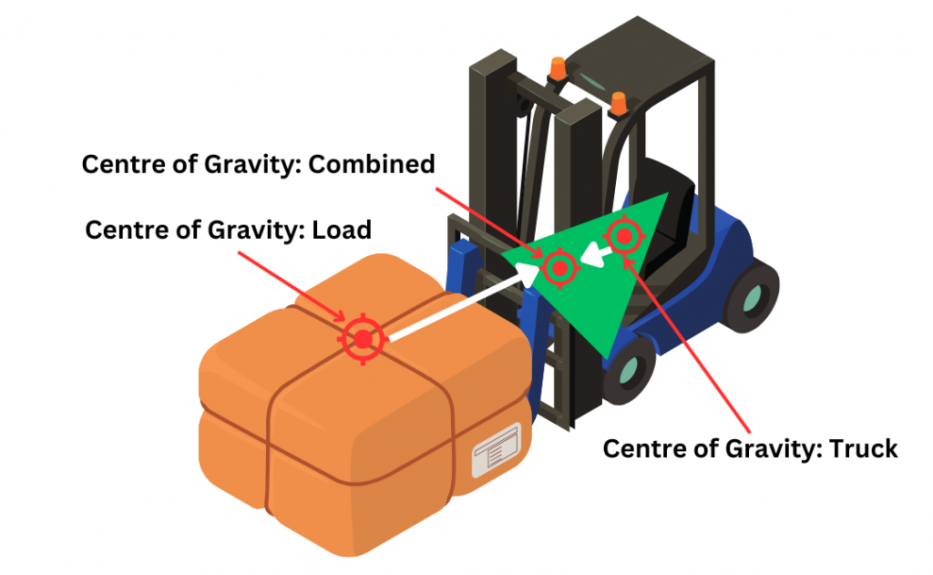
For a perfectly square load, the center of gravity is at the load’s direct center.
The center of gravity is the imaginary point where all of an object’s weight is concentrated. In forklifts, there are two centers of gravity to consider:
- Unloaded Forklift: The center of gravity is typically located directly beneath the operator’s seat.
- Load: The center of gravity depends on the load’s shape and weight distribution. For a perfectly square load, the center of gravity is at the load’s direct center. However, irregularly shaped loads will have a center of gravity that may not be centrally located.
When the load’s center of gravity is uneven, it can create an imbalance that may affect forklift stability.
What Is Combined Center of Gravity?
When a forklift picks up a load, the individual centers of gravity for both the forklift and the load merge into a single, combined center of gravity.
Importance of Combined Center of Gravity
The location of this combined center of gravity within the stability triangle determines whether the forklift remains stable or is at risk of tipping. If the combined center of gravity shifts too far outside the stability triangle, the forklift may become unstable.
By understanding the stability triangle and how the combined center of gravity works, operators can better ensure safe handling and operation of forklifts under different load conditions.
3. What Is the Difference Between Residual Capacities and Nominal Capacities?
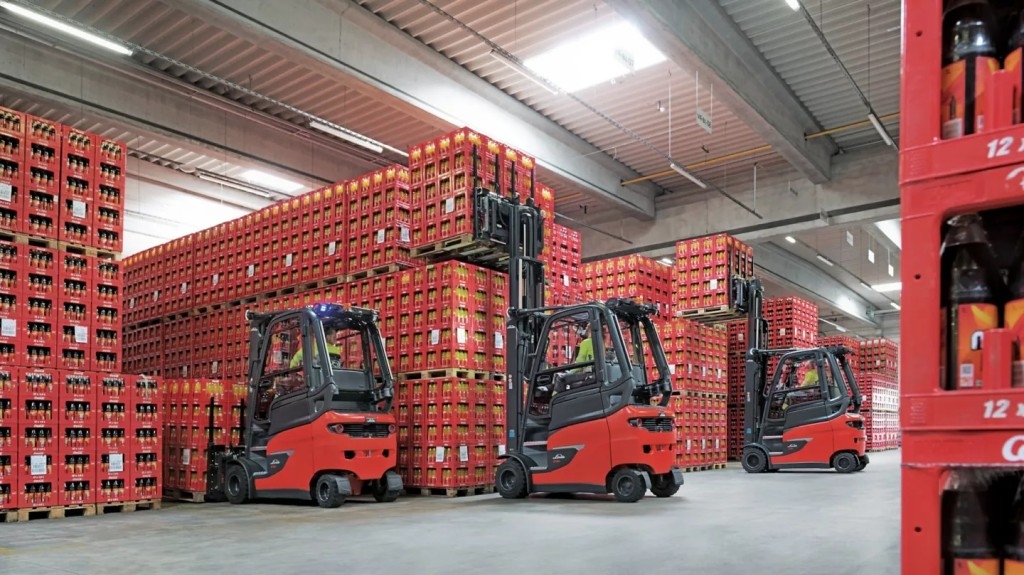
Residual Capacities vs Nominal Capacities: These two terms define a forklift’s lifting capabilities under different conditions.
Understanding the distinction between nominal and residual capacities is crucial for safe and efficient forklift operation. These two terms define a forklift’s lifting capabilities under different conditions.
Nominal Capacity
Nominal capacity refers to the maximum weight a forklift can lift to a predetermined height, assuming the load’s center of gravity is at a specific point, known as the standard load center. This capacity is determined under ideal conditions and is typically specified by the manufacturer. The Nominal Capacity of a forklift is BEFORE any attachments are added and is how much this forklift with no attachments can lift off the ground – but not up to the top of the reach of the mast. A 2.5 tonne forklift can lift 2.5 tonnes Nominally – but not necessarily to the height you require – nor with any attachments.
For example, a forklift might have a nominal capacity of 2.0 tonnes at a 500 mm load center, meaning it can lift up to 2.0 tonnes if the load’s center of gravity is 500 mm from the vertical face of the forks. But if you add an attachment, and if you are lifting 12 ft high for example the truck will NOT be able to lift 2 tonnes any longer.
Residual Capacity
Residual capacity is the actual lifting capacity of a forklift in a given situation, which may be less than the nominal capacity. Factors such as lifting the load above the predetermined height or having a load center further away than the standard (ie because of an attachment like a sideshifter or clamp) can reduce the forklift’s capacity.
The use of attachments, the size, shape and weight distribution of the load, and the lift height can all impact the residual capacity. Therefore, it’s essential to assess the residual capacity for each specific lifting scenario to ensure safe operation. You can learn more about load centers in Section 4 of this post.
Key Factors Affecting Residual Capacity
Several factors can influence a forklift’s residual capacity:
Lifting Height
As a forklift lifts a load higher, its lifting capacity decreases. This occurs because the center of gravity of the load shifts upward and forward. Eventually, the load’s center of gravity may extend beyond the forklift’s stability triangle, increasing the risk of tipping.
Attachments
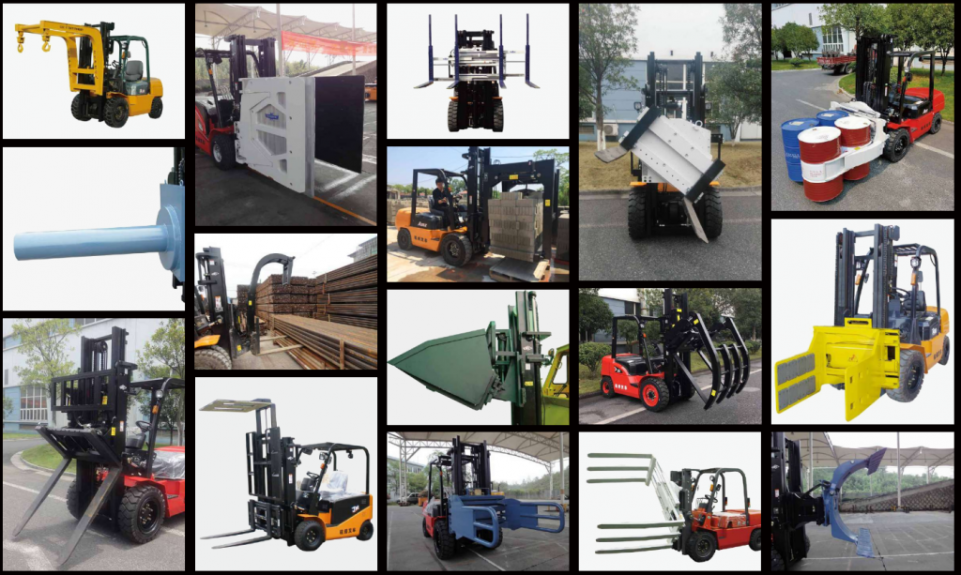
Residual Capacities vs Nominal Capacities: Attachments add weight to the forklift, reducing its ability to lift heavy loads.
Adding attachments to a forklift can lower its lifting capacity for two main reasons. First, attachments add weight to the forklift, reducing its ability to lift heavy loads. Second, attachments extend the load center forward, increasing the load moment and further reducing lifting capacity.
Load Length
If a load exceeds the default 24-inch load center, the forklift’s lifting capacity decreases. Longer loads shift the combined center of gravity forward, which compromises stability and reduces the amount of weight the forklift can safely lift.
Load Distribution
Forklifts are rated for lifting loads with evenly distributed weight. When a load is unevenly distributed, the center of gravity shifts forward or sideways, causing the forklift to lose lifting capacity and stability. To maintain safety, always ensure that the heaviest part of the load is closest to the fork face.
Wheel and Tire Type
The type, size, and configuration of a forklift’s tires directly affect its lifting capacity. For example, dual tires and wide tires increase lifting capacity by enhancing the stability of the forklift. Similarly, cushion tires provide better capacity retention than pneumatic tires.
Battery Weight
In electric forklifts, the battery plays a key role in stabilization. If the battery is too light, it may not provide enough counterweight to maintain stability. It’s important to ensure that the battery weighs at least as much as the minimum weight specified on the forklift’s data plate.
Fork Wear
As a forklift’s forks wear down, its lifting capacity is reduced. Each 10% of erosion on the fork’s heel thickness can reduce lifting capacity by up to 20%. Regular inspection and replacement of worn forks and tires are crucial for maintaining the forklift’s safety and performance.
Importance of Understanding Residual Capacity
Relying solely on a forklift’s nominal capacity can lead to unsafe operating conditions if real-world factors aren’t considered. By understanding and calculating the residual capacity, operators can make informed decisions, ensuring that the forklift is used within its safe lifting limits for each specific task. This practice helps prevent accidents, equipment damage, and potential injuries in the workplace.
In summary, while the nominal capacity provides a baseline for a forklift’s lifting capabilities under ideal conditions, the residual capacity offers a more accurate measure of what the forklift can safely handle in various real-world scenarios. Operators should always consider residual capacity to maintain safety and efficiency in their material handling operations.
4. What Are Load Centers and Why Do They Matter?
Understanding load centers is essential for forklift operators because they directly impact a forklift’s stability, as well as its nominal and residual lifting capacities. If the load is not properly centered or balanced, the forklift is at risk of tipping over. Let’s explore what load centers are and how they relate to safe forklift operation.
What Is a Load Center?
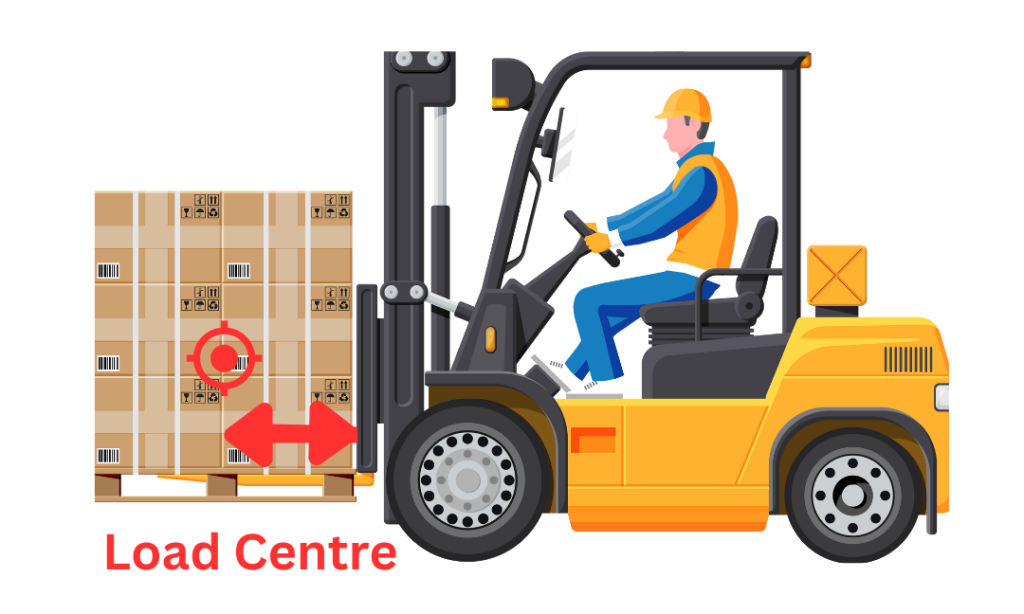
The load centre is the distance from the face of the forks to the load’s centre of gravity.
The Occupational Safety and Health Administration (OSHA) defines a load center as “the distance from the face of the forks to the load’s center of gravity.” The load center measurement begins at the fork’s vertical face and extends to the midpoint of the load’s weight distribution.
In a perfectly square load, such as a pallet of evenly distributed bricks, the center of gravity is at the direct center of the load. For irregularly shaped or unevenly distributed loads, the center of gravity may be offset, which can cause instability.
How Load Centers Affect Forklift Balance
A forklift balances two key forces:
- Counterweight: The heavy metal weight at the rear of the forklift that counterbalances the load on the forks.
- Load: The object being lifted, whose weight and position directly affect the forklift’s center of gravity. When a load is lifted, the combined center of gravity (the combined weight of the forklift and load) shifts toward the pivot point at the front axle. If the load is too heavy or too far from the fork face, the center of gravity may move beyond the stability triangle, increasing the risk of tipping.
How Load Centers Relate to Nominal and Residual Capacities
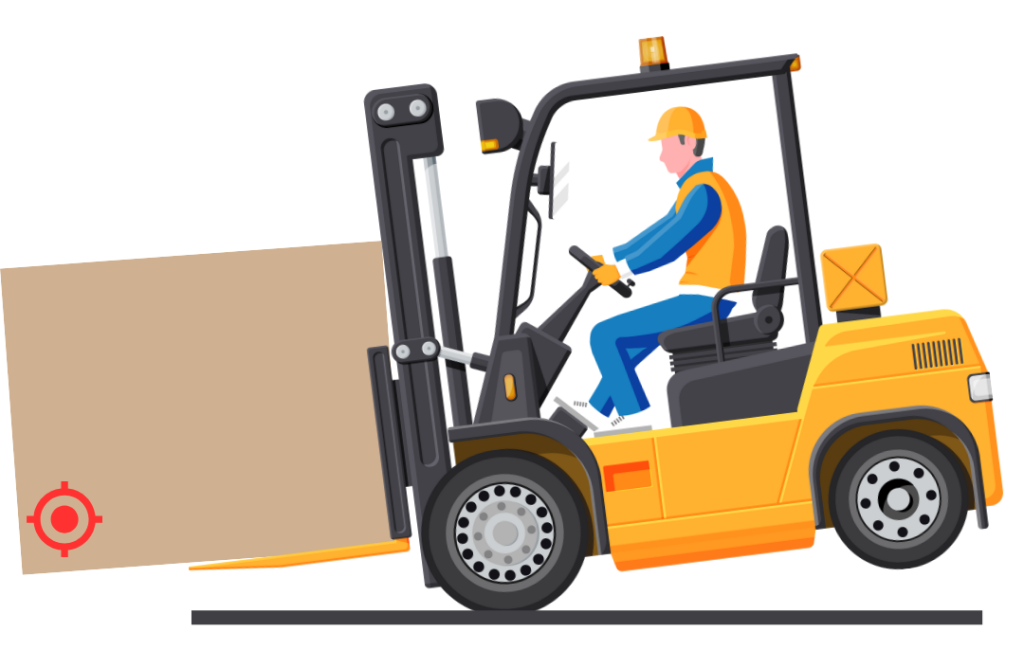
The farther the load’s center of gravity moves from the fork face, the lower the residual capacity becomes.
Nominal Capacity:
Nominal capacity is the maximum weight a forklift can lift under ideal conditions with a specified load center (e.g., 500 mm from the fork face). If the load’s center of gravity stays within this standard distance, the forklift should be stable.
Residual Capacity:
When the load center exceeds the nominal distance or if attachments are used, the forklift’s actual lifting capacity decreases. The farther the load’s center of gravity moves from the fork face, the lower the residual capacity becomes.
The Teeter-Totter Analogy
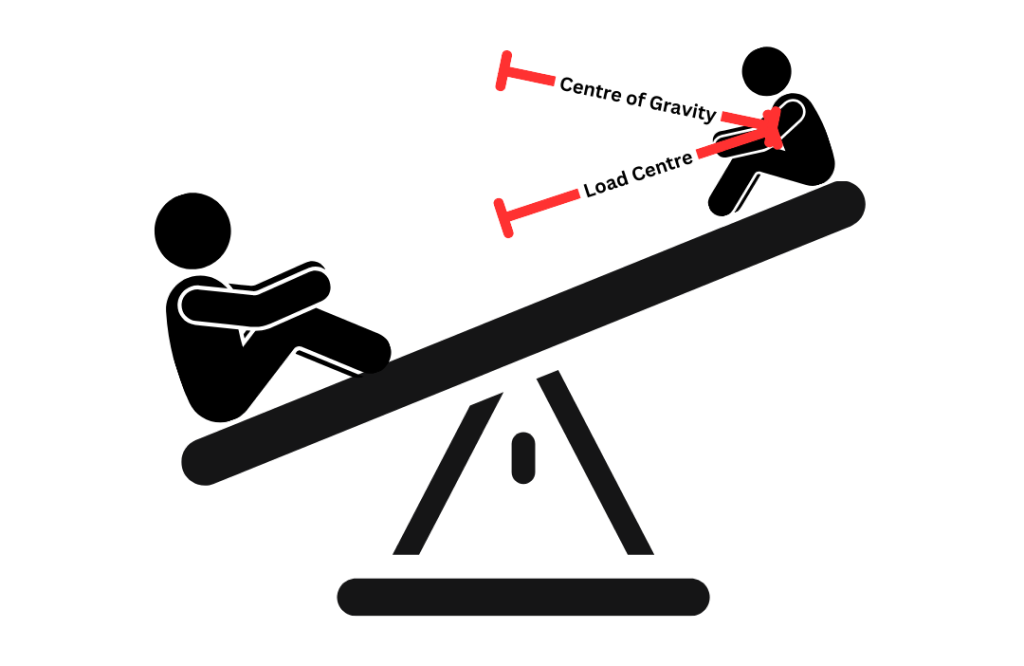
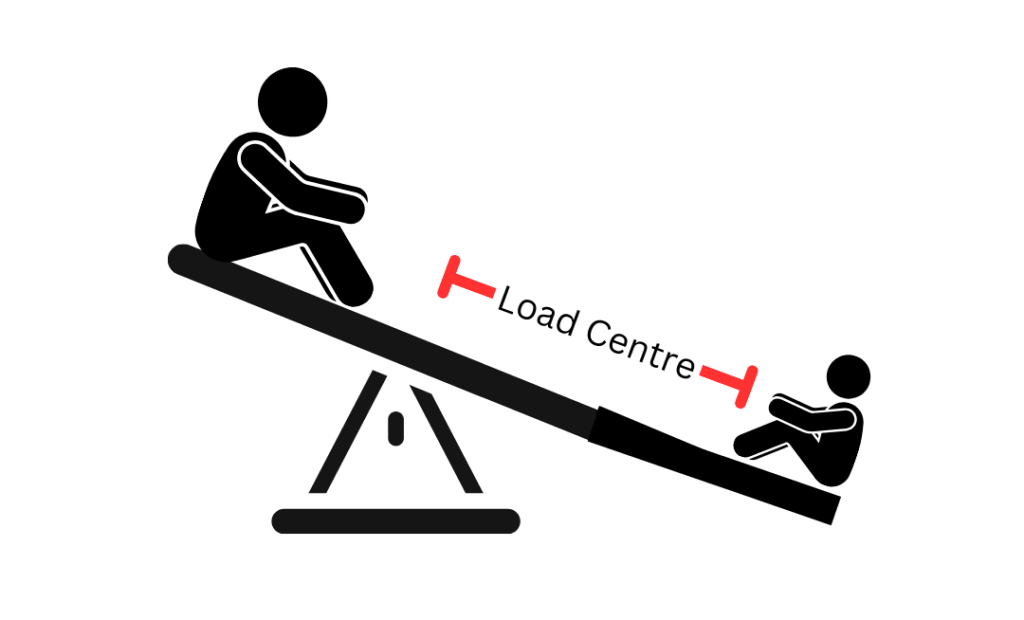
A lighter person can tip the teeter-totter if they move far enough beyond the pivot point.
Imagine a teeter-totter with a 225-pound person on one side and a 125-pound person on the other. If both are seated at equal distances from the pivot point, the teeter-totter remains balanced. However, if the 125-pound person moves farther from the pivot, they can tip the teeter-totter despite their lower weight.
This same principle applies to forklifts. A load that is too far from the fork face (the pivot point equivalent) can cause the forklift to tip, even if the load’s weight is within the forklift’s nominal capacity.
Ensuring Proper Load Distribution
To maintain stability and prevent accidents, it’s critical to:
- Ensure loads are evenly distributed and centered.
- Keep the load’s center of gravity within the forklift’s rated load center distance.
- Regularly check the forklift’s capacity plate for load center and weight guidelines.
By understanding how load centers influence forklift stability and capacity, operators can make informed decisions to ensure safe and efficient material handling.
5. How to Read Your Forklift Capacity Plate
Understanding how to read your forklift’s capacity plate is essential to ensuring safe and efficient operation of your forklift. The capacity plate contains critical information about your forklift’s lifting capabilities, including load centers, lifting heights, and weight limitations. Here’s how to interpret the key elements of the plate:
Visual Indicators: Load Centers and Lifting Heights
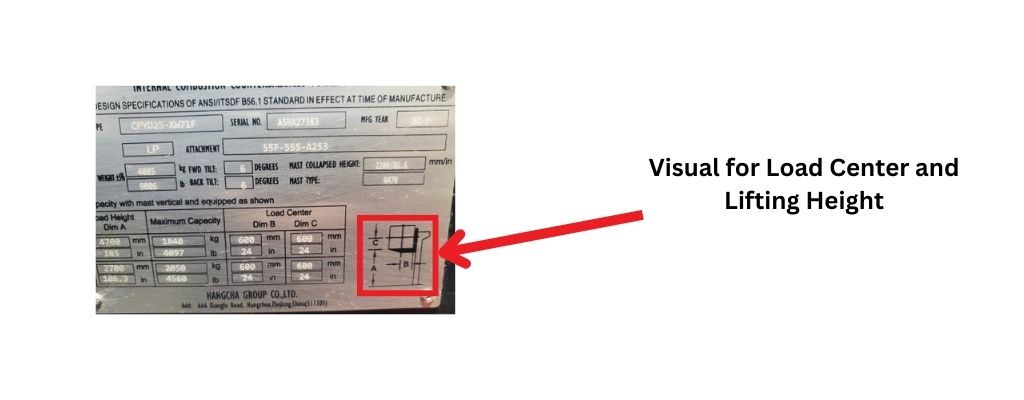
Each data plate may look slightly different, but the information that you will need to determine your forklift’s lifting capabilities will be found on your forklift’s data plate. The above image is a Hangcha data plate. At the bottom right corner of this forklift’s capacity plate, you’ll see an image that will give you a visual representation of important forklift metrics:
Side-View Image: This drawing shows the forklift’s mast, forks, and load from the side.
Letters: This image has the letters (A, B, C) labeled on them. These correspond to specific values in the table on the left-hand side of the plate. Let’s break down each one:
Load Centers (B and C):
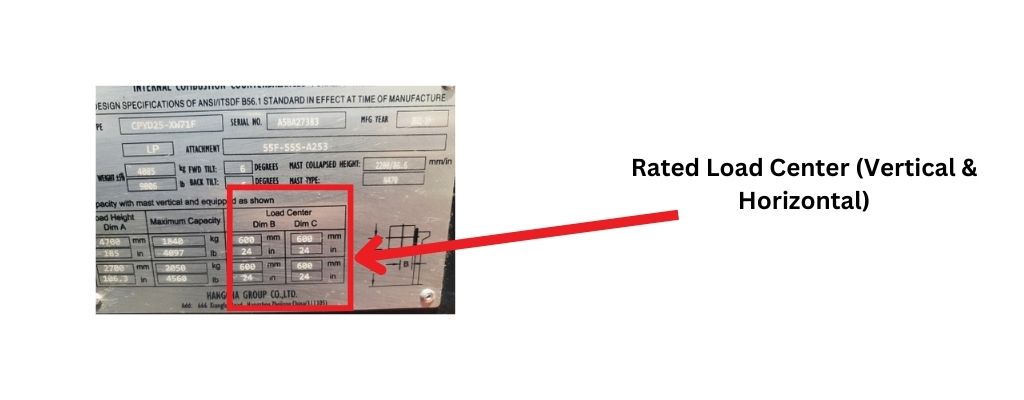
The letters “B” and “C” represent the load center, which is the distance from the face of the forks to the center of gravity of the load. These are critical for understanding how much weight the forklift can safely lift at different distances from the forks.
In the example above, both “B” and “C” show a 24-inch (600 mm) load center, indicating that the forklift is rated for loads where the weight is evenly distributed 24 inches from the face of the forks. If the load center exceeds 24 inches, the forklift’s lifting capacity will decrease.
Lift Height (A)
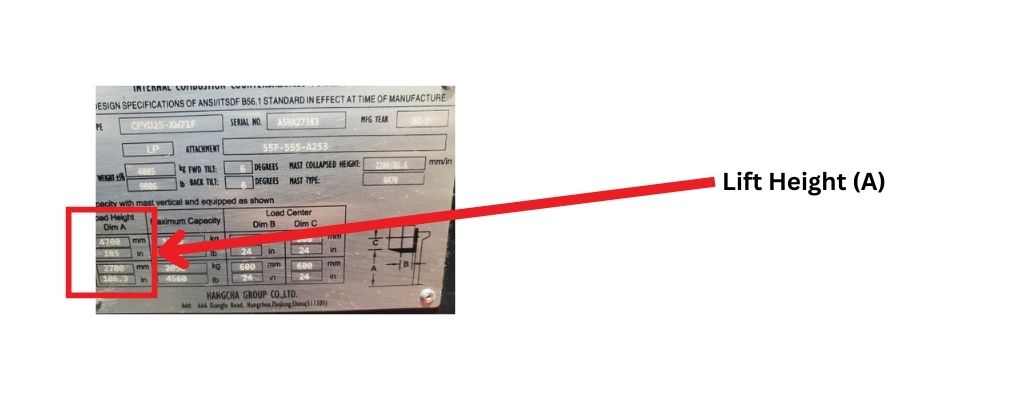
The letter “A” represents the lift height, or the maximum height the forklift can lift the load. In this example, the table shows a lift height of 185 inches (4,700 mm). The lift height is critical because lifting at greater heights shifts the forklift’s center of gravity and reduces its stability, which in turn decreases its lifting capacity.
Putting It All Together: Example Capacity Calculation
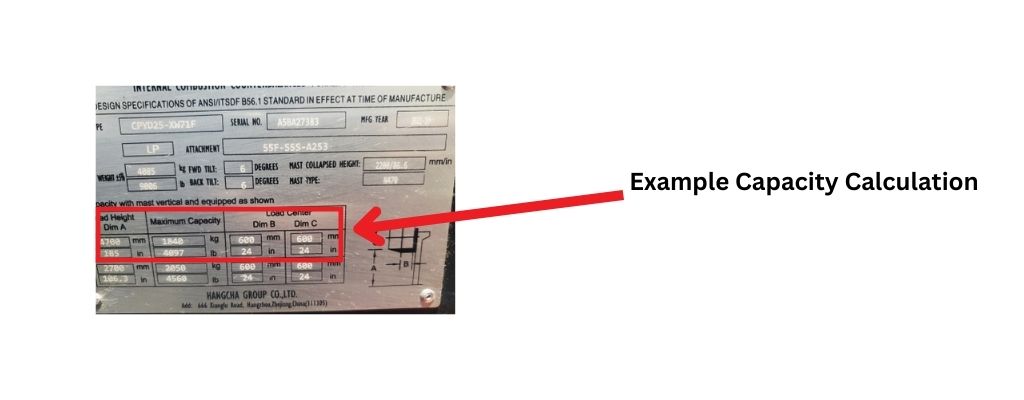
Let’s look at an example to understand how the values on the capacity plate combine to determine lifting capacity:
For a forklift with a 24-inch load center and a lift height of 185 inches, the forklift can safely lift 4,097 lbs as long as the load’s center of gravity is at 24 inches.
Impact of Attachments on Capacity
Attachments can also reduce a forklift’s lifting capacity. For example, a sideshifting fork positioner attachment may reduce the forklift’s capacity by up to 150 lbs at a 24-inch load center and 850 lbs at a 30-inch load center. It’s essential to account for any attachments when determining your forklift’s operational capacity.
By properly understanding how to read the capacity plate and the information it provides, you can ensure safe operation and avoid overloading your forklift.
6. What Is the Capacity of Your Forklift: Calculation
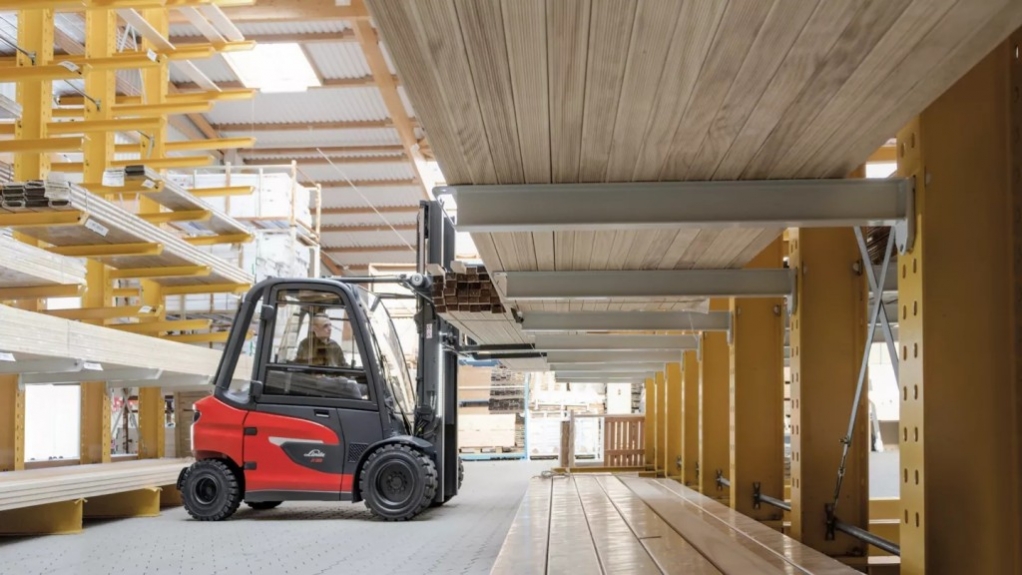
Residual Capacities vs Nominal Capacities: If the load’s center of gravity matches the forklift’s rated load center, the calculation is straightforward.
Now that we’ve explored how to read your forklift’s capacity plate, it’s time to address how to calculate the load capacity of your forklift, especially when the load center differs from the rated load center. While this process can seem complicated, the math is relatively simple once you understand the basic principles.
Calculating Load Capacity at Rated Load Center
If the load’s center of gravity matches the forklift’s rated load center, the calculation is straightforward. You simply refer to the capacity data tag to see what weight your forklift can safely handle at the specified load center.
For example, if the data plate indicates that your forklift can lift 5,850 lbs. to a height of 187 inches at a 24-inch load center, you would follow that specification as the forklift’s maximum lifting capacity for this load.
When the Load Center Is Different
What happens if the load’s center of gravity is different from the rated load center? In such cases, the capacity decreases. Fortunately, OSHA provides a method to calculate the actual forklift capacity based on the ratio of the rated load center to the actual load center.
The Forklift Capacity Calculation Formula
The formula you’ll use to estimate your forklift’s actual load capacity is as follows:
Rated Load Center ÷ Actual Load Center x Truck Rated Load Capacity = Actual Forklift Capacity
To better understand how this works, let’s look at an example:
Example Calculation:
Imagine you have a 5,000 lb. forklift with a rated load center of 24 inches. If your actual load center is 27 inches, here’s how you’d calculate the capacity:
Rated Load Center (24 inches) ÷ Actual Load Center (27 inches) = 0.889
0.889 x 5,000 lbs. (Truck Rated Load Capacity) = 4,445 lbs.
This means your forklift can safely lift 4,445 lbs. at a 27-inch load center, which is less than its rated capacity due to the increased distance between the forks and the load center.
The Linde Advantage: Linde Forklifts Last Longer
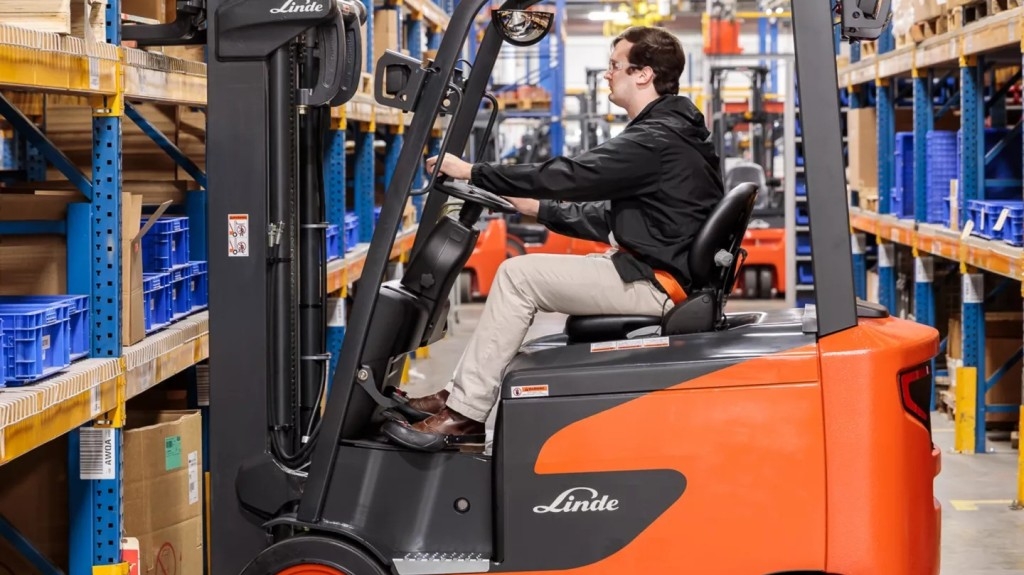
Linde forklifts last twice as long as other brands.
When investing in a forklift, longevity and productivity are key considerations—and that’s where Linde truly excels. Unlike other brands built to a 10,000-hour lifespan, Linde forklifts are engineered to last an impressive 20,000 hours, doubling their operational life and providing exceptional long-term value. This remarkable durability helps justify Linde’s premium price tag, offering unmatched performance and reliability over time.
Why Linde Lasts Longer
Linde forklifts are a testament to German engineering excellence, known for precision and quality. Key design features, like the hydrostatic drive system, eliminate traditional transmission components, reducing wear and tear and enhancing efficiency. Additionally, Linde’s engines operate at lower RPMs compared to competitors, minimizing engine wear and extending their lifespan significantly. These thoughtful innovations ensure that Linde forklifts are built not just to work but to last.
Unmatched Productivity
Durability is only part of the equation. According to TÜV Nord, an independent vehicle inspection and consulting firm, Linde forklifts are up to 22% more productive than any other manufacturer. This productivity boost means you’ll accomplish more in less time, maximizing efficiency and reducing operational costs.
With Linde, you’re not just investing in a forklift—you’re investing in a high-performance machine that delivers unmatched durability, efficiency, and long-term savings.
Looking for a New Forklift? Contact Ri-Go
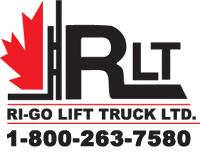
If you are in the market for a new forklift, contact us. Our knowledgeable staff can help you choose the perfect one for your needs.
Since 1977, Ri-Go Lift Truck has been serving customers in Ontario and Quebec with everything they need for material handling. We are committed to providing you with quality service and a high level of customer satisfaction.
We are your authorized dealer for the following top brands:
- Linde Lift Trucks, Power Pallet Trucks, Tow Tractors and Stackers
- Hangcha Forklifts Full Lineup of Electric & IC Equipment
- Blue Giant Lift Trucks and Pallet Movers
- Komatsu Forklifts and Reach Trucks
- Mariotti Lift Trucks – The Worlds Smallest Lift Truck
- Baoli Lift Trucks
- Advance Sweepers and Scrubbers
- Skyjack Genie Booms and Scissor Lifts

In addition to our authorized distributorships, we can also provide you with:
- Large selection of used forklifts
- Operator Training Department – open 7 days a week
- Parts Departments – over 1.4 million dollars of parts on hand for all makes and models
- Service Department – highly trained technicians
- Leasing and Rentals
No matter what your material handling needs are, we can help. Contact us today to let us know how we can be of service.
What Our Customers Think…
“Excellent people and excellent service. I highly recommend them. Always exceptionally respectful and professional.” – Bill Flesias